Inside a Vermeister product
What's inside a Vermeister product?
Each Vermeister product doesn’t just contain the ingredients of a recipe, it also has the story of the daily commitment of love and passion for what we do, which begins with the search for the best raw materials and the formulation of recipes in line with the highest quality standards, while also characterized by the extensive work required for controlling every single detail.
All this activity is regulated by the UNI EN ISO 9001:2015 CERTIFIED QUALITY MANAGEMENT SYSTEM, with which we have defined rigorous and distinguished procedures to ensure absolute constancy of production.
Over 300 different raw materials are used in our production process. Constant inspection over the entire supply chain for raw materials and any consumables. A network of certified suppliers with whom over time we have established close cooperative relationships; important synergies for the development of raw materials with customized characteristics at our specific request
RAW MATERIAL QUALITY CONTROL
(the main ones are mentioned)
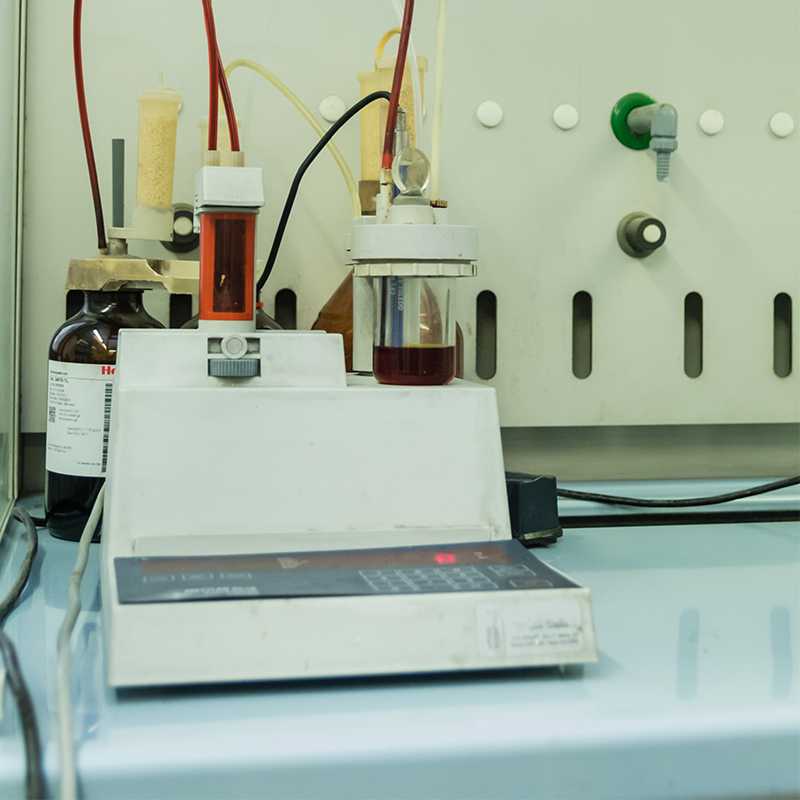
Degree of humidity
Control of the exact degree of humidity by way of a Karl-Fischer titrator, to protect the stability of the hygrosetting products.
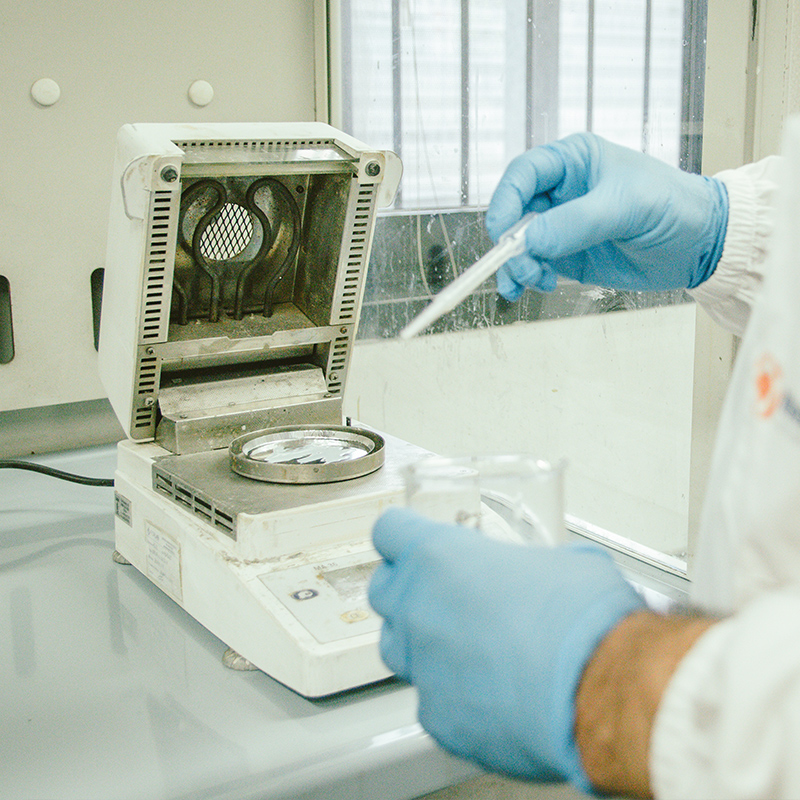
Solid content
Control of the solid content by way of thermal balance.
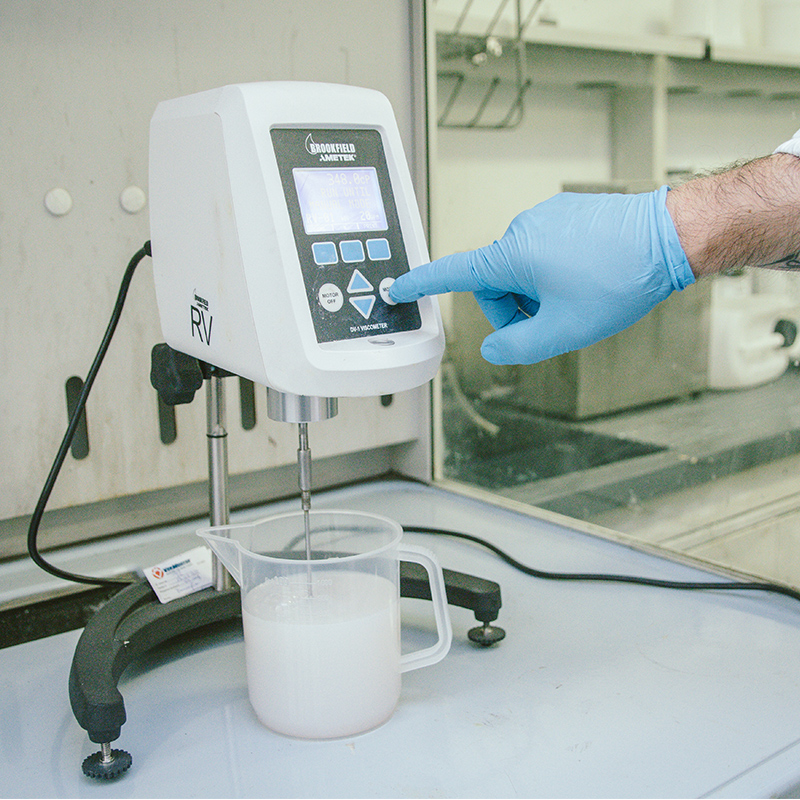
Viscosity
Control of viscosity and rheological characteristics by way of a Brookfield viscometer.
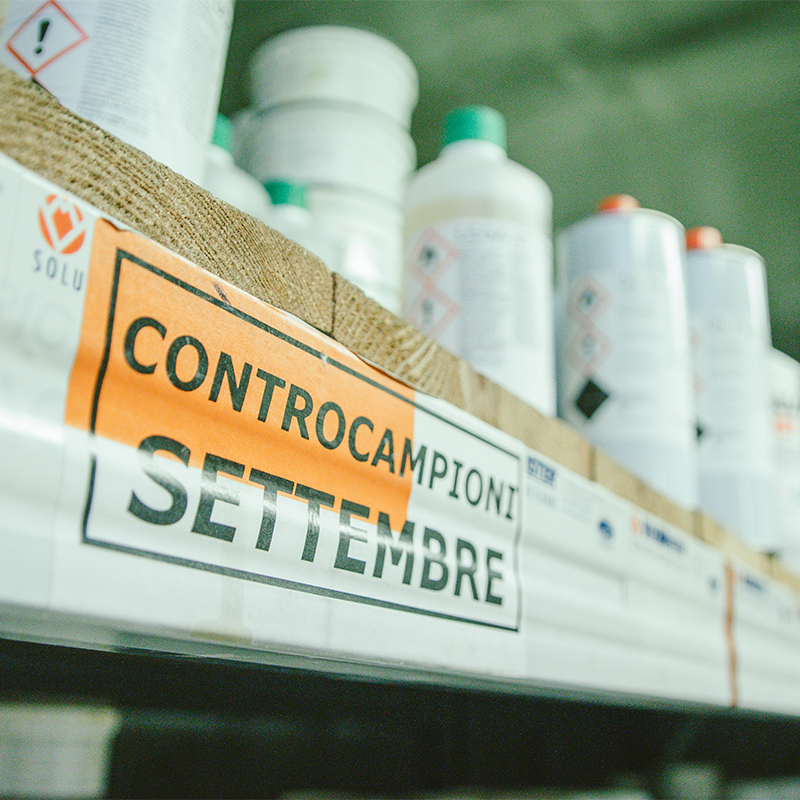
A sample of each individual incoming raw material is stored for 1 year at a controlled temperature, in order to manage its control and then guarantee its quality throughout the life of the material. During this period of time, we are able to faithfully reproduce each batch with the same precise raw materials used.
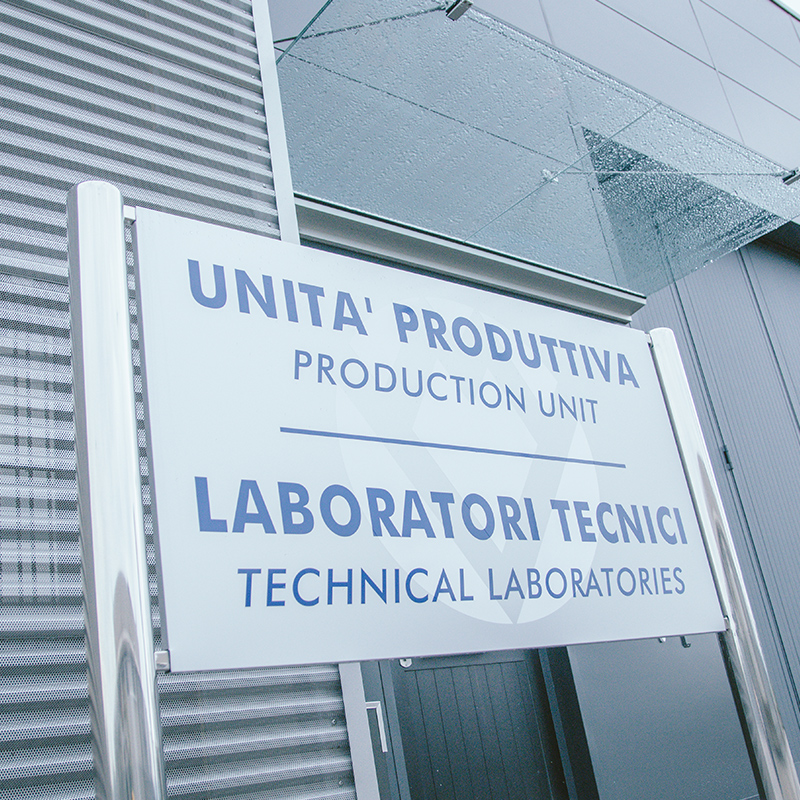
Over 150 items in the catalog, all designed and produced at the Mornico al Serio plant.
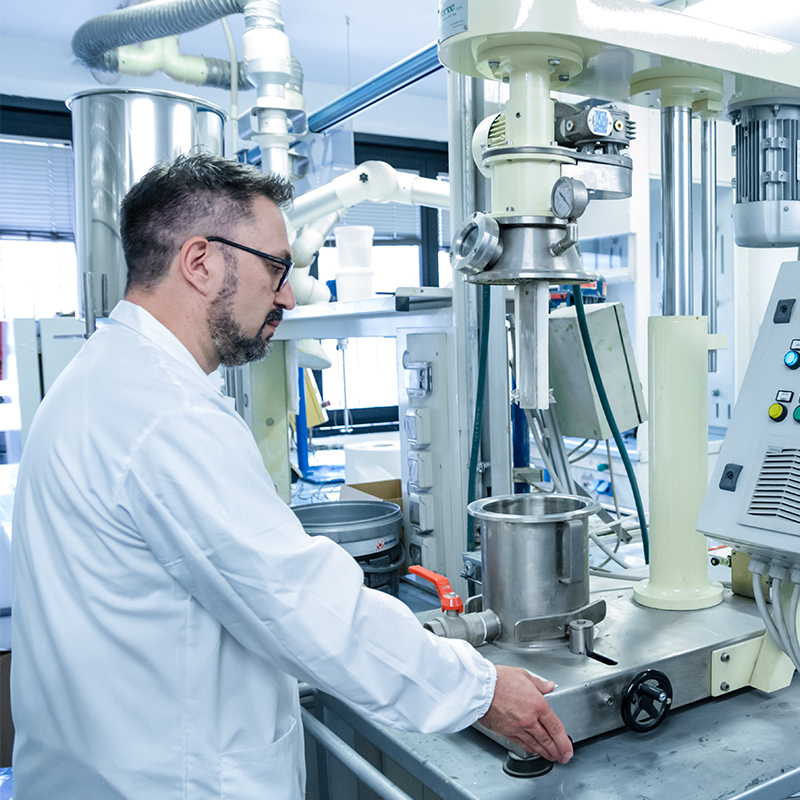
Each product is first manufactured in the Research & Development laboratory. From pilot batches to the industrial scale, with the precise purpose of predicting every possible scenario during the industrial production process.
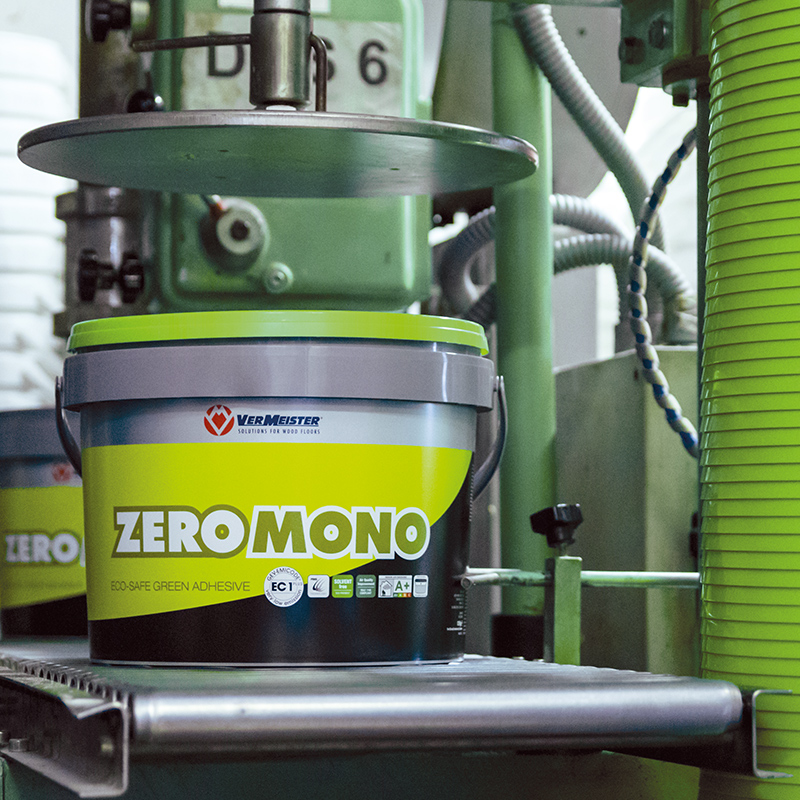
Never lose sight of our only goal: WOODEN FLOORS. 2,500,000 kg/ year of adhesives and more than 1,000,000 liters of coatings designed and produced at the Mornico al Serio plant.
COATING QUALITY CONTROL
1 test carried out in the intermediate phase on each production batch. 10 or 12 tests, depending on the product, are carried out at the end of each production batch before packaging and sale.
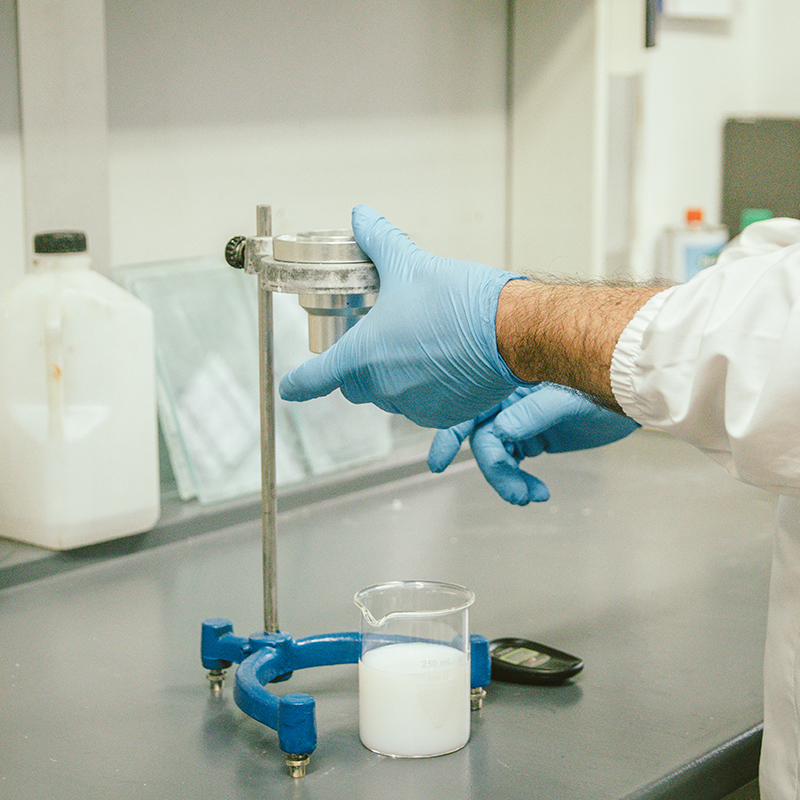
Viscosity
Control of the viscosity of coatings from the production process to the final package using a Ford cup.
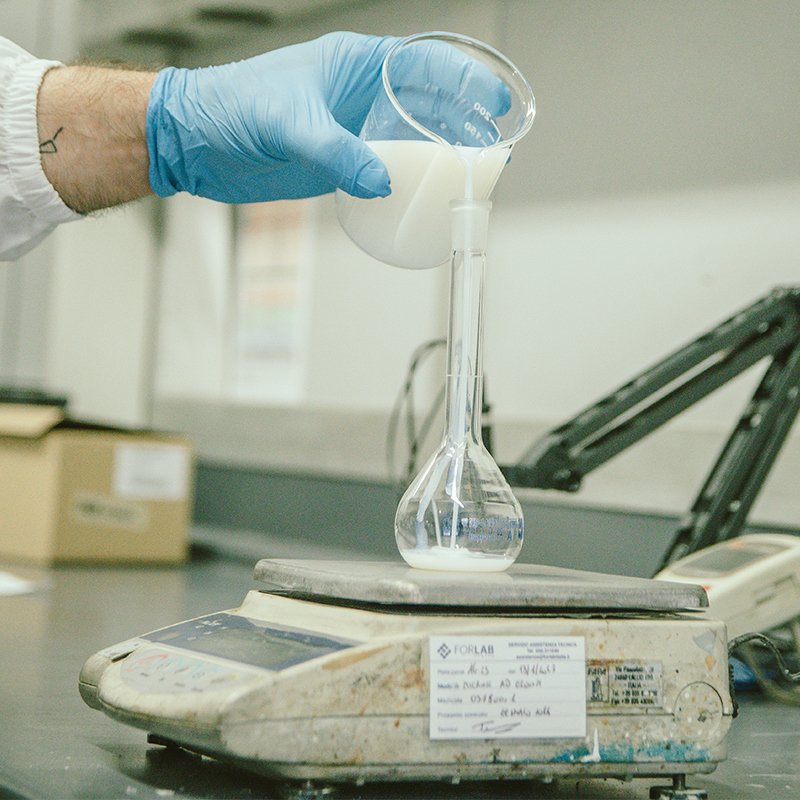
Density - solid content
Fundamental controls to measure the weight/volume ratio and quantify the percentage of resin that remains on the wooden element to guarantee coverage and protection.
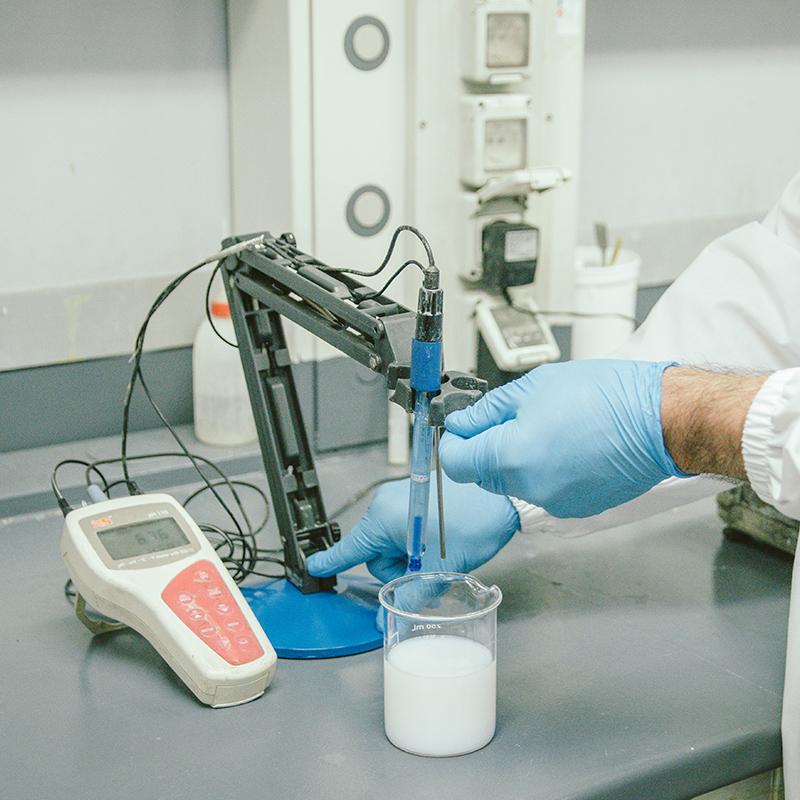
pH control
The use of self-cross-connecting resins (S-XL) requires control of the pH levels of the blends during production processes and before packaging.
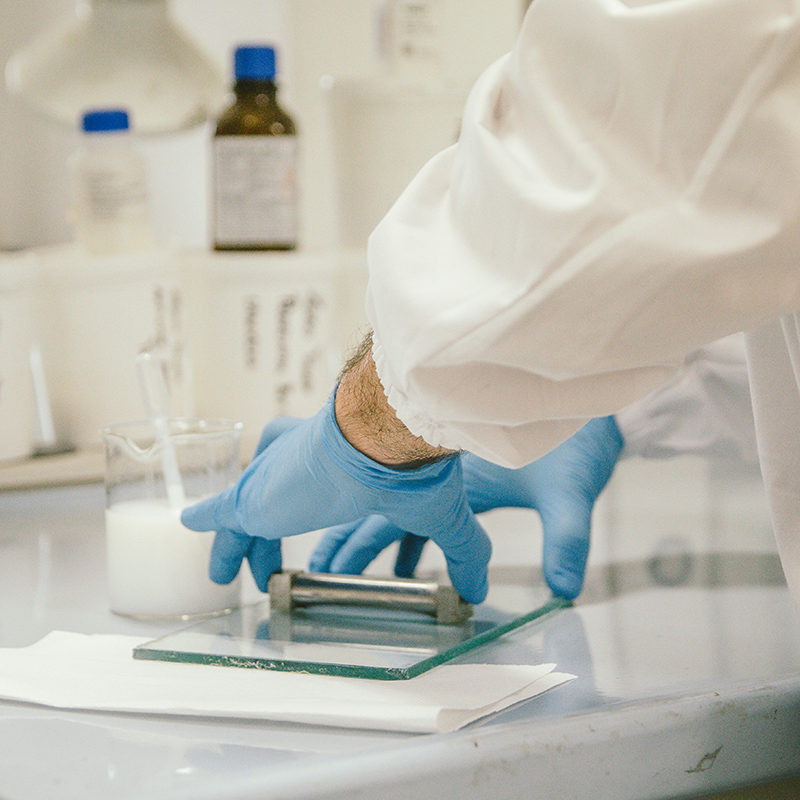
Control glass
Visual control on glass, to monitor the state of the dispersions at any stage of processing.
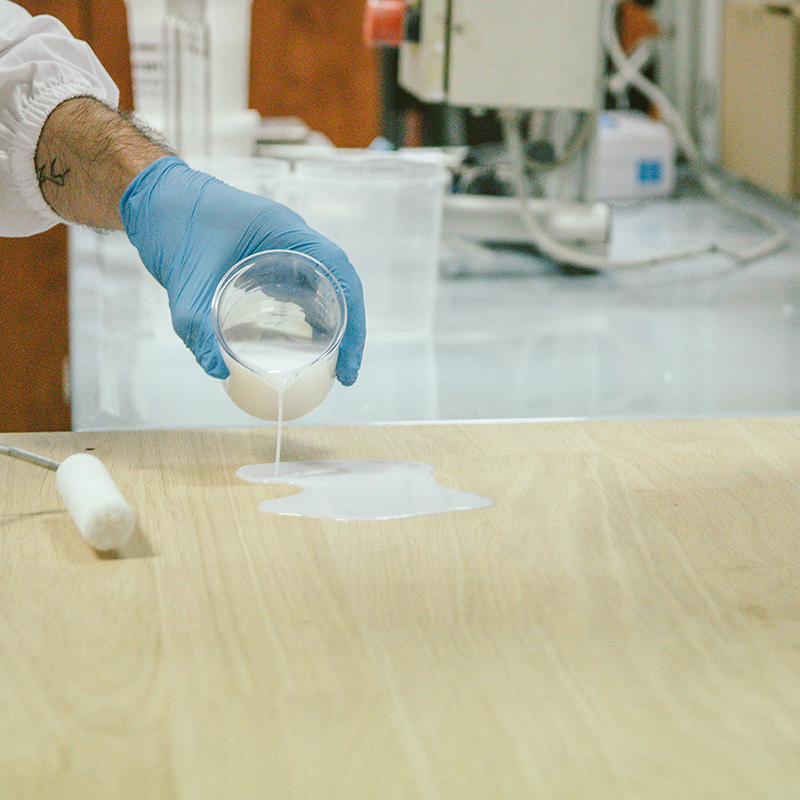
Application on wood
Control designed to recreate, in a small way, the application of any coating product on a suitable wooden support.
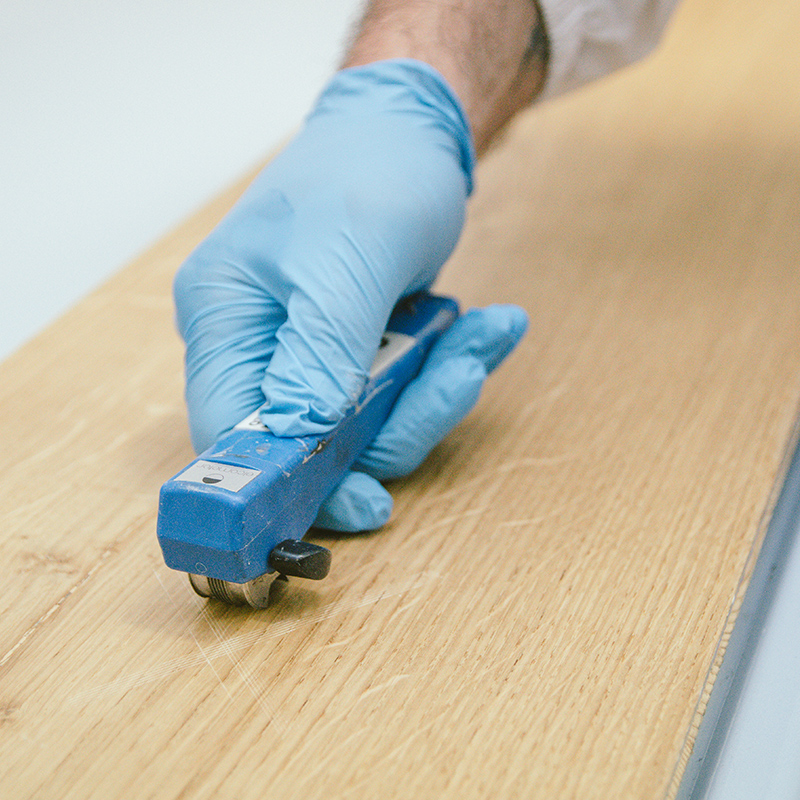
Adhesion check (Cross Cut)
Adhesion check (Cross Cut), to assess the suitability of the overlaps between layers of coatings also depending on the timing with and without sanding.
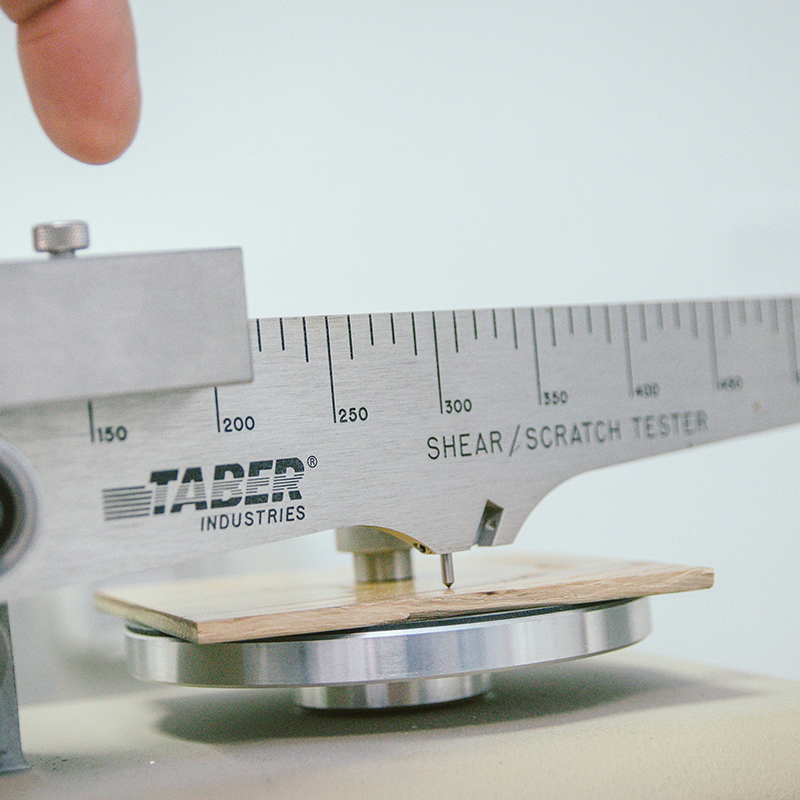
Scratch Resistance
Scratch Resistance, to measure the degree of of the coating film’s resistance to incisions, executed with a standard diamond tip.
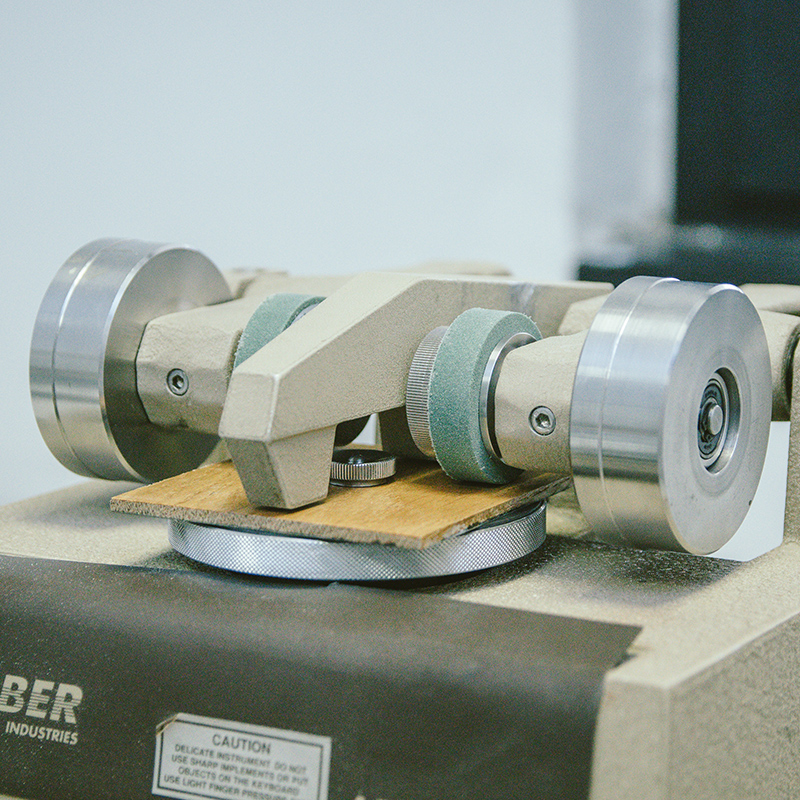
Abrasion resistance
Abrasion resistance, to verify the finish film’s resistance to abrasion stress by means of a special pair of abrasive wheels that turn on the sample analyzed, removing coating.
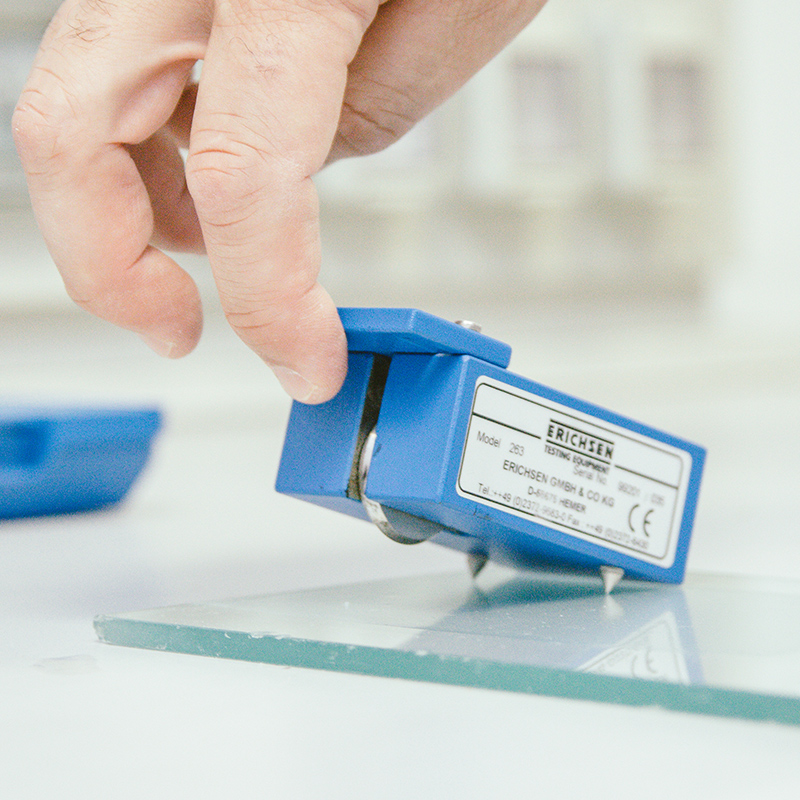
Buchholz hardness
Simulation test of impact on the coatin
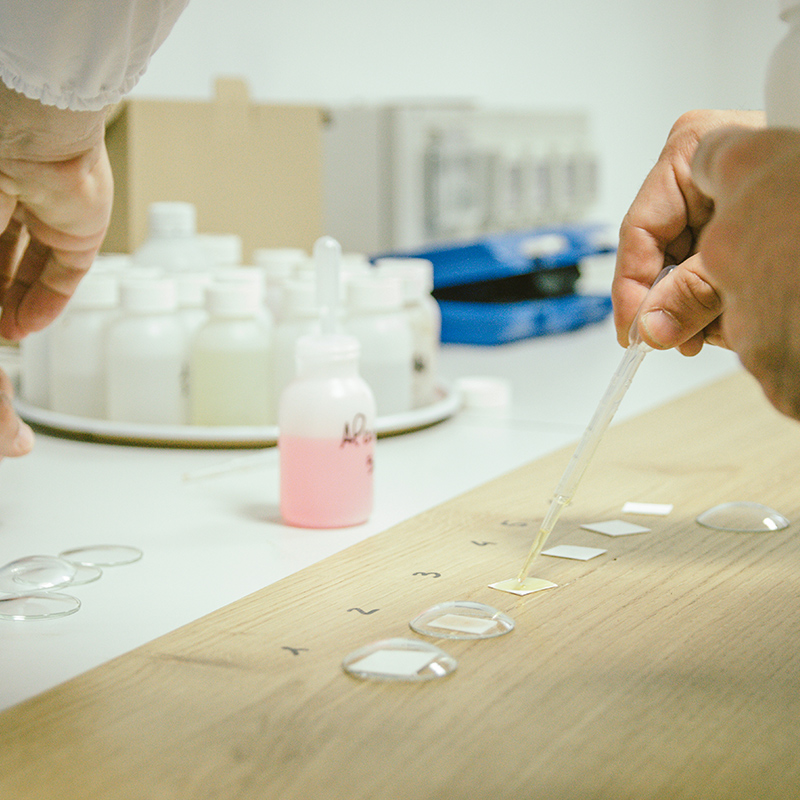
Chemical resistances
Evaluation of the resistance to liquids, of various kinds and aggressiveness, essential for inserting the wooden floor in any environment, residential and commercial.
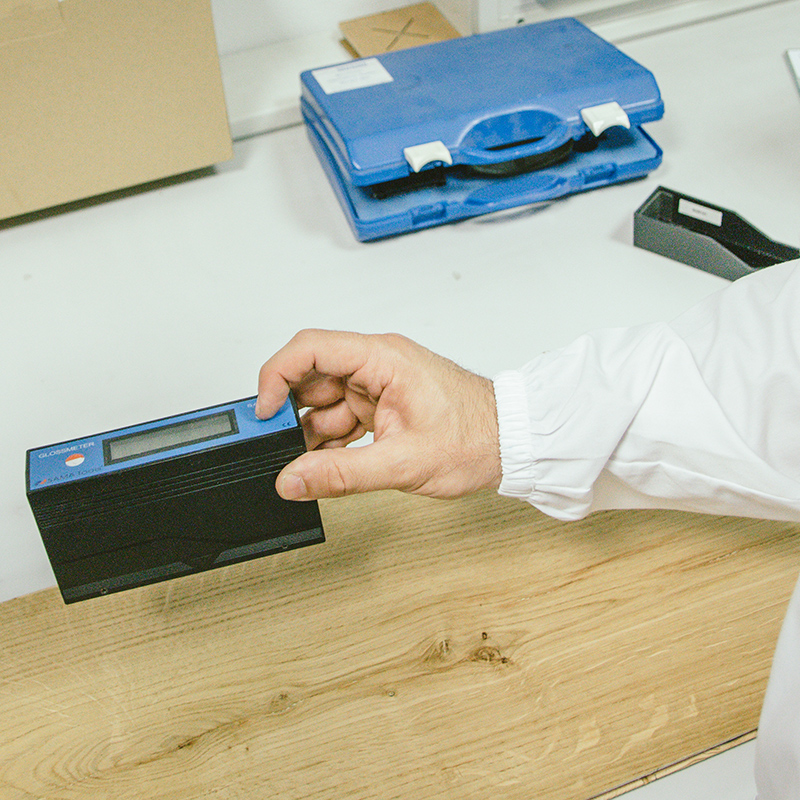
Sheen
Sheen control, to measure the degree of gloss that will define the final appearance of the coating product.
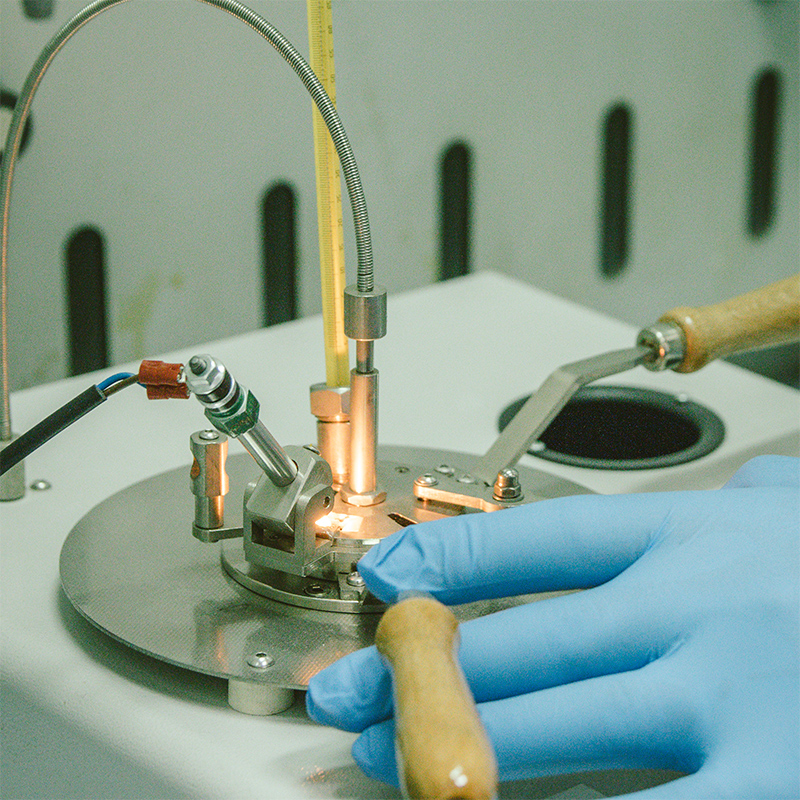
Flash-point
Flash-point. For solvent-based products, the flash point is checked to define the correct labeling.
All tests are repeated on each batch 30 – 60 – 90 days from the date of manufacture
ADHESIVE QUALITY CONTROL
1 test carried out in the intermediate phase on each production batch. 5 tests are carried out at the end of each production batch before packaging and sale.
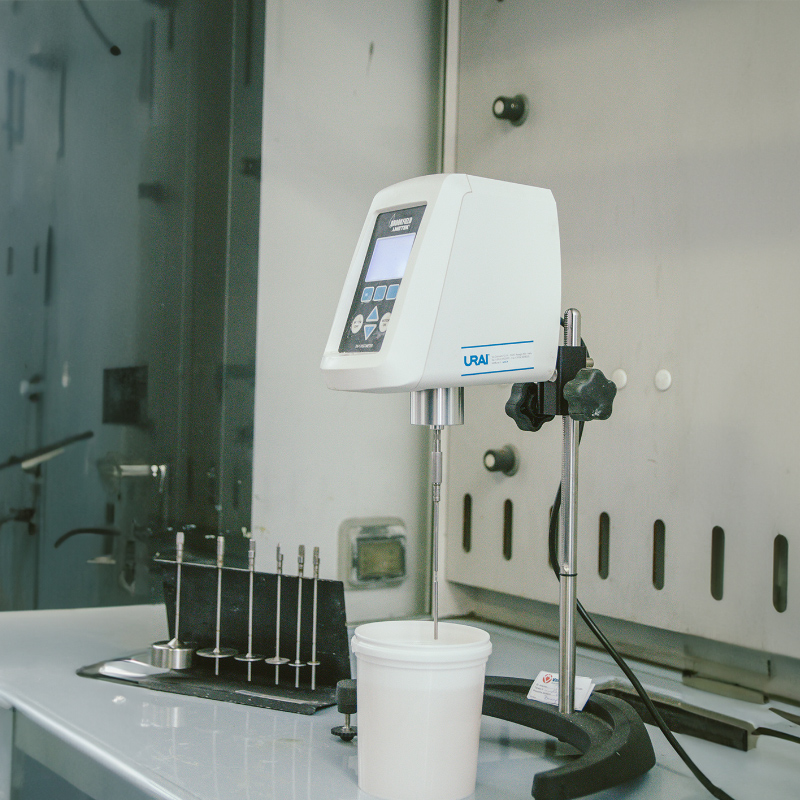
Viscosity-rheology
Viscosity-rheology control, using a Brookfield viscometer, to define all the rheological characteristics of an adhesive, on each individual component and after the possible mixing of the two components.
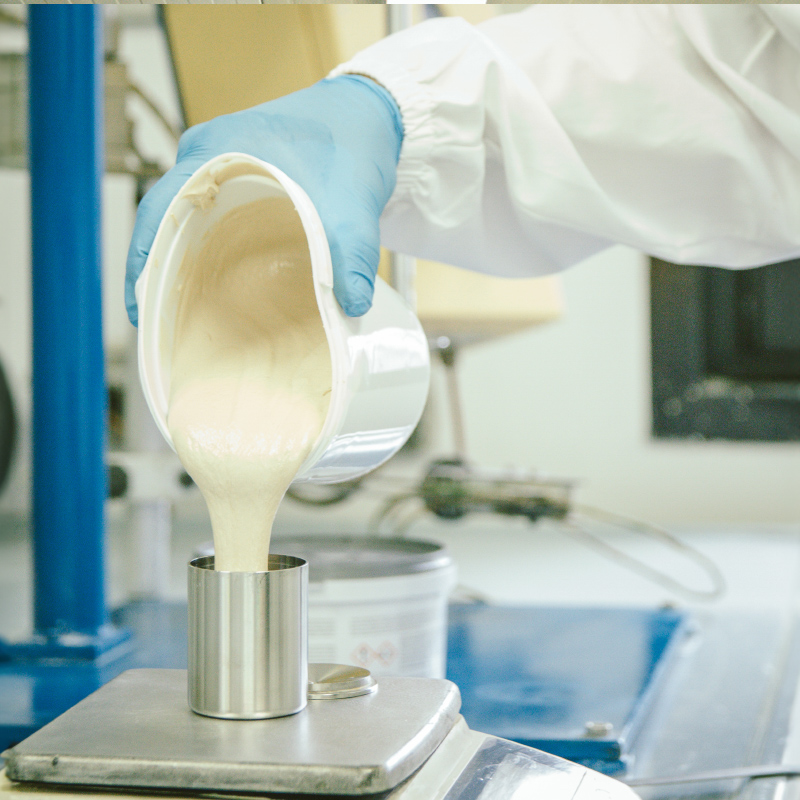
Density
Density control, using a special pycnometer, for evaluating the weight/volume ratio. Appearance, in adhesives, determines the metric yield of the product.
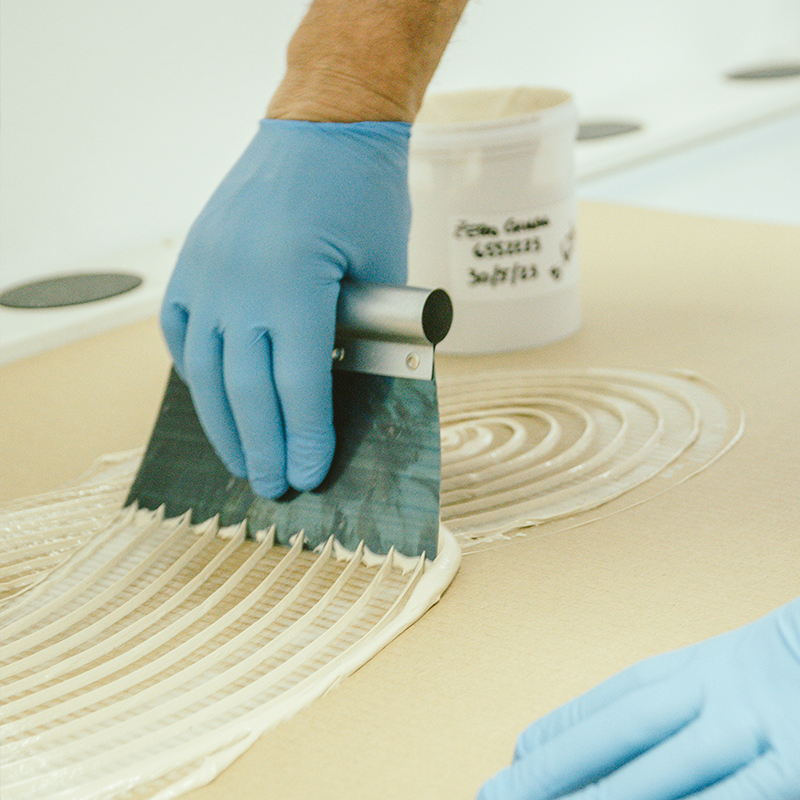
Pot-life control and hardening curve
Pot-life control and hardening curve, to simulate all the phases of preparation and subsequent application of an adhesive and monitor all the “vital” parameters to guarantee correct implementation.
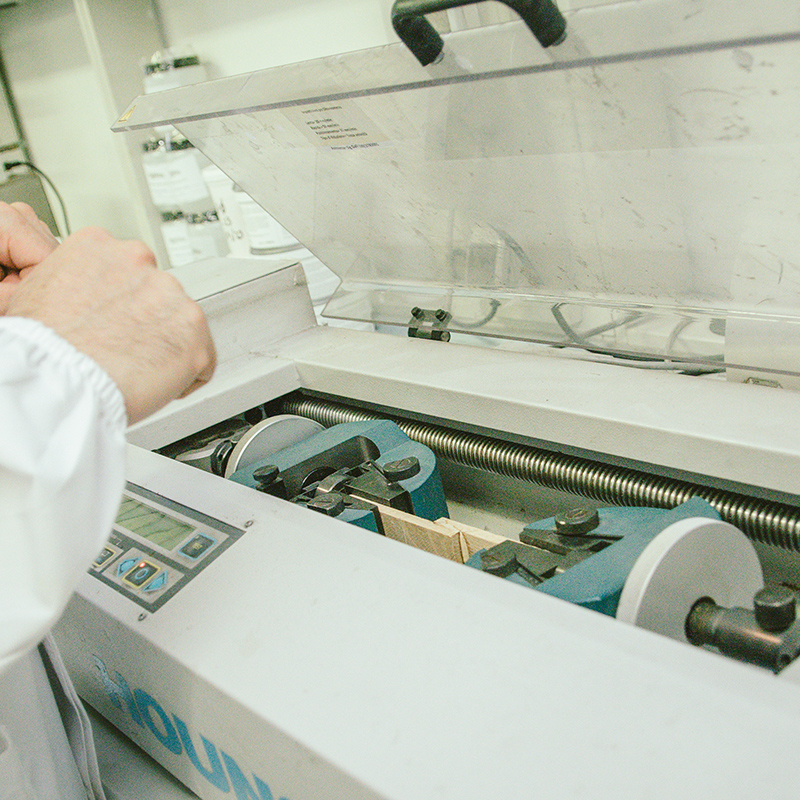
Tensile strength control
Tensile strength control: the importance of tear-resistance of a wooden floor adhesive for safe and durable bonding on any support.
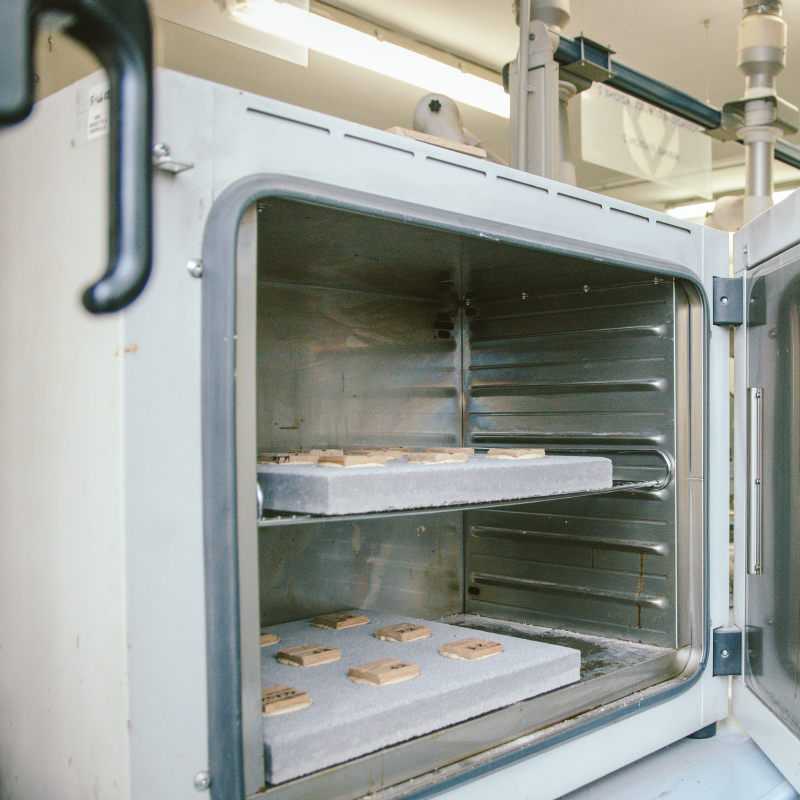
Evaluation of thermal stability (41 days at T=90°C)
Evaluation of thermal stability (41 days at T=90°C) to analyze and compare old and new regulations and define the best standards to pursue. Batch
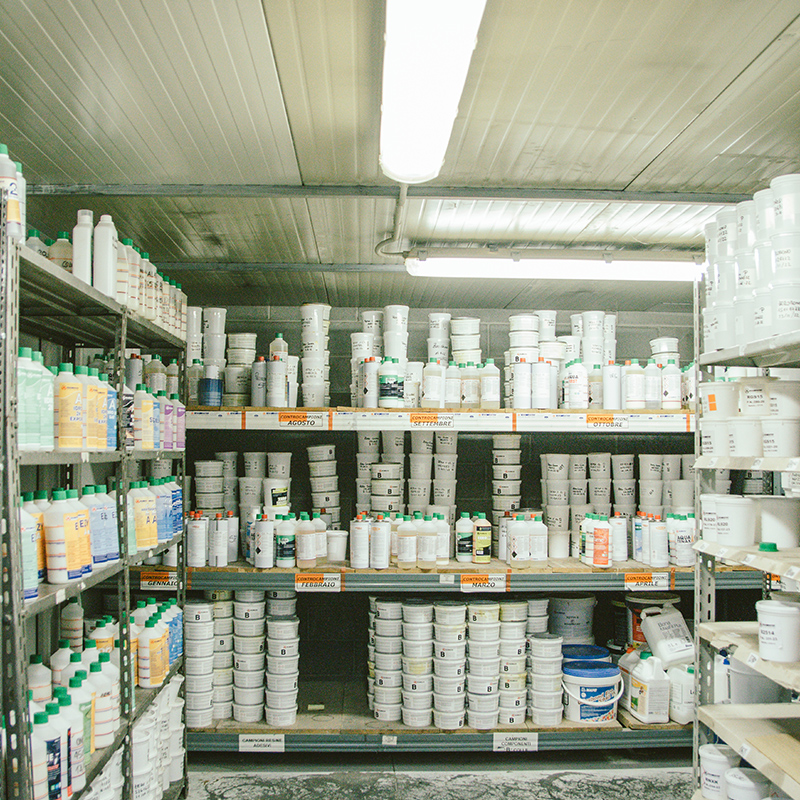
Batch samples
A sample of each individual production batch is kept for 1 year at a controlled temperature; a quality management process essential for monitoring all corporate processes.
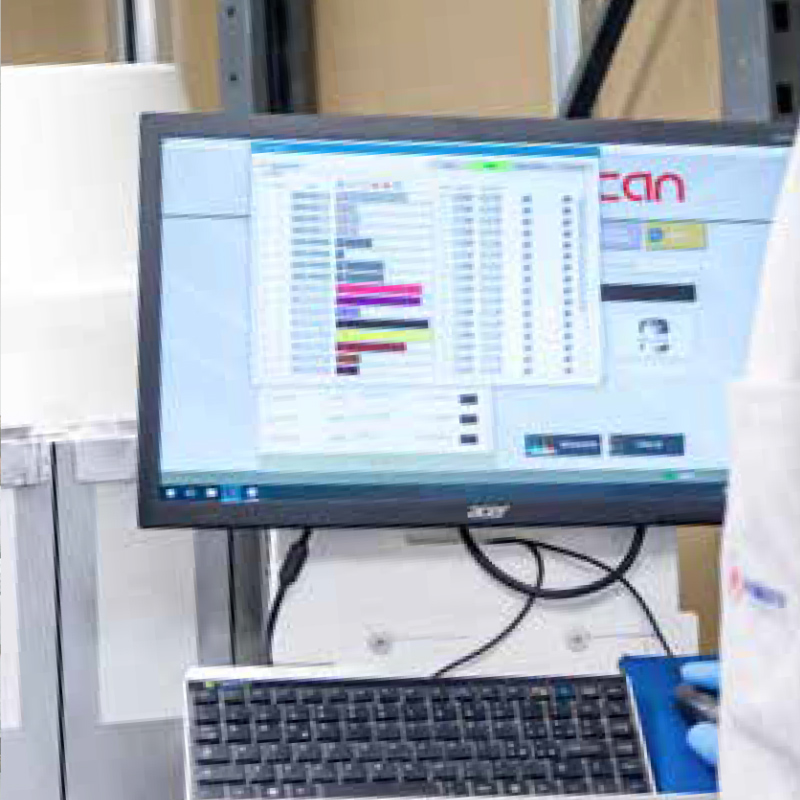
Chromotherapy
46 colours available + infinite “on-demand” colours, prepared inhouse in our Colour Laboratory.
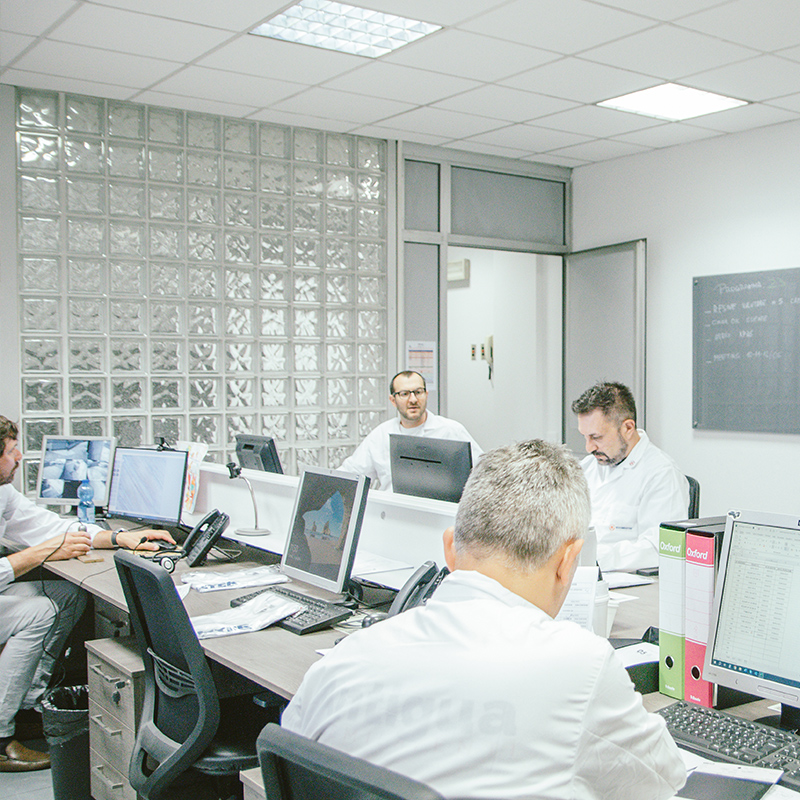
Technical support
Tensile strength control: the importance of tear-resistance of a wooden floor adhesive for safe and durable bonding on any support.